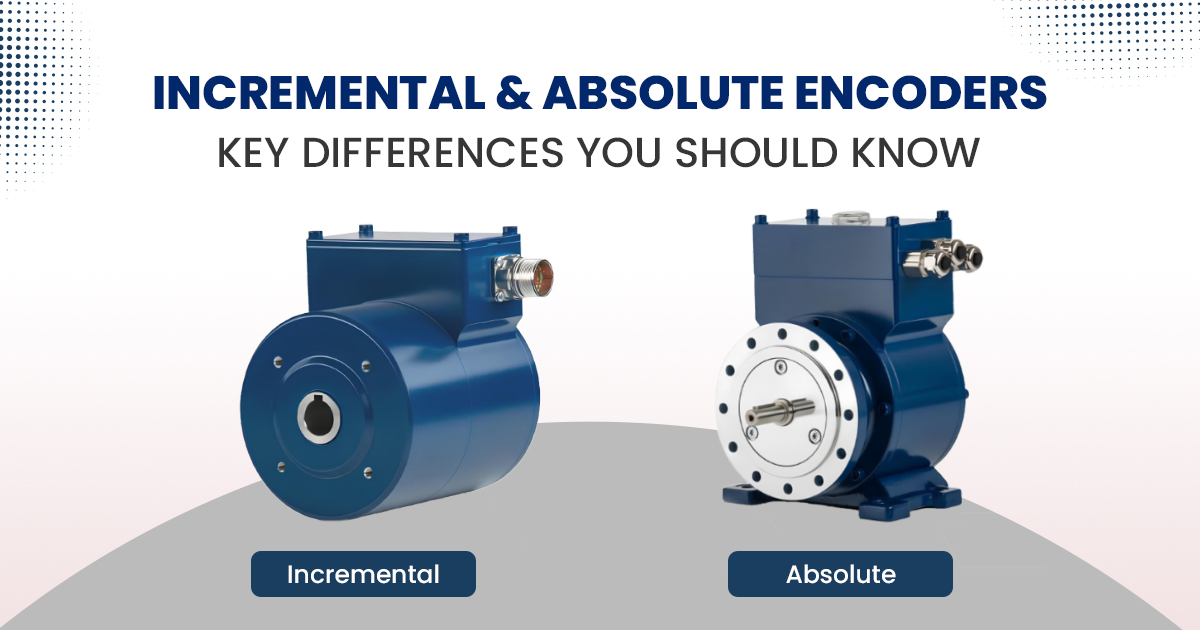
Incremental & Absolute Encoders: Key Differences You Should Know
- April 18, 2025
- by
- bhavik@bcreative.in
Consider working with heavy industrial machinery where even the smallest position error can shut down production. That’s where encoders took place. These tools convert motion into readable signals that help machines know the exact position, speed, and direction. But not all encoders are the same. The two most common types of encoders are incremental encoders and absolute encoders. The right encoder can help you in achieving accuracy and safety within your operations.
Let us see how each of these kinds of encoders functions, for what purpose they are used, and when one would be better suited to use than the other.
How Does an Encoder Work?
An encoder is an electromechanical device that provides feedback on motion, specifically velocity, position, and direction. It functions through creating signals based on the movement of a shaft. Signals are also sent to a control system, and it computes data and makes a decision accordingly.
What Is the Use of Absolute Encoders?
Absolute encoders keep track of the accurate position of a shaft, even in the case of power loss. There is a unique digital code for each position, so that the encoder does not need to be calibrated every time it is powered on.
Key Features of Absolute Encoders:
- Retain position data after shutdown
- Deliver unique position values for every angle
- Ideal for complex or multi-turn applications
Common Applications:
- Cranes and Hoists
- Hoisting Gear
- Steel and Rolling Mills
- Mining Operations
- Renewable Energy
If your machinery requires exact positioning and must resume its work without recalibration after a power outage, absolute encoders are the practical choice.
What Are Incremental Encoders Used For?
Incremental encoders produce pulses as the shaft rotates. The system monitors these pulses to indicate motion and direction, but not position. In the event of a power loss, the system loses its position and has to be reset to zero when restarted.
Key Features of Incremental Encoders:
- Provide relative position data
- Require a reference point on startup
- Provide high-speed response for real-time feedback
Common Applications:
- Conveyor systems
- Machine Tools
- Heavy industrial equipment
They are ideal when continuous power is expected and fast motion feedback is the priority over precise position retention.
What is the Difference between Absolute and Incremental Encoders?
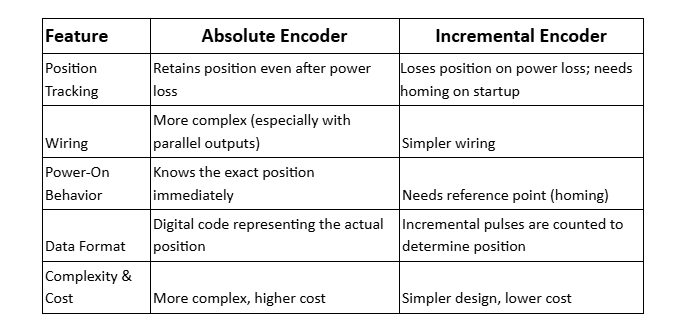
Absolute encoders have the key benefit of delivering exact position data and retaining it even if there’s a power outage. This makes them ideal for applications where precision and reliability are critical. On the other hand, incremental encoders are more budget-friendly and easier to set up, but they need a reference point to determine position and will lose their data if power is lost. The choice between the two depends on the specific application requirements.
What Is the Application of Encoders?
Encoders are used where there is a need for precise control of motion. The following are the principal application fields of encoders:
- Industrial automation
- Robotics and motion control
- Motor feedback systems
- Elevator and lift control
- Braking systems in heavy machinery
You should select an encoder according to your needs. If position memory and safety are vital, use absolute encoders. If cost and rapid response are more vital for you, use an incremental encoder.
Understanding the difference between incremental and absolute encoders isn’t just technical jargon, it directly affects how safely and efficiently your machines operate. In industrial brake systems and automation, businesses from various sectors count on Emco Precima for reliable encoder solutions designed for challenging environments.
Choose your encoder based on what your system needs today, and what it might demand tomorrow.
Still unsure which encoder suits your machine best? Contact us today!